Introduction to Glass Balls in Industrial Use
The Role of Glass Balls in Modern Industry
Glass balls play a crucial role in many industries today. These tiny spheres are more than just decorative items. They have unique properties that make them valuable in various applications. Glass balls are strong, durable, and resistant to chemicals. They can withstand high temperatures and pressure.

In manufacturing, glass balls are used for grinding and polishing. They help create smooth surfaces on metals and other materials. In the automotive industry, they're used in reflective paints for road signs. Glass balls are also important in electronics, where they're used in circuit boards.
These small spheres are perfect for filtration systems. They can trap tiny particles while allowing liquids to pass through. This makes them useful in water treatment plants and other filtration processes. Glass balls are also used in renewable energy, helping to improve solar panel efficiency.
Key Industries Utilizing Glass Balls
Many industries rely on glass balls for their operations. Here are some key sectors:
- Automotive: Used in reflective paints and coatings
- Aerospace: Found in lightweight composite materials
- Electronics: Used in circuit boards and displays
- Pharmaceutical: Used in drug delivery systems
- Food and Beverage: Used in filtration processes
- Energy: Found in solar panels and wind turbines
- Mining: Used for ore separation and purification
The automotive industry uses glass balls in paints to make cars more visible at night. In aerospace, these balls help create strong but lightweight materials for aircraft. Electronics manufacturers use them to make circuit boards and touchscreens.
In the pharmaceutical industry, glass balls are used to coat pills and in drug delivery systems. The food and beverage sector uses them for filtering liquids. In the energy sector, they help improve the efficiency of solar panels and wind turbines.
Manufacturing Processes of Glass Balls
The Production Process of Glass Balls
Making glass balls is a precise process. It starts with high-quality silica sand. This sand is melted in furnaces at very high temperatures, often over 1500°C. The molten glass is then formed into small droplets. There are different methods to create these droplets.
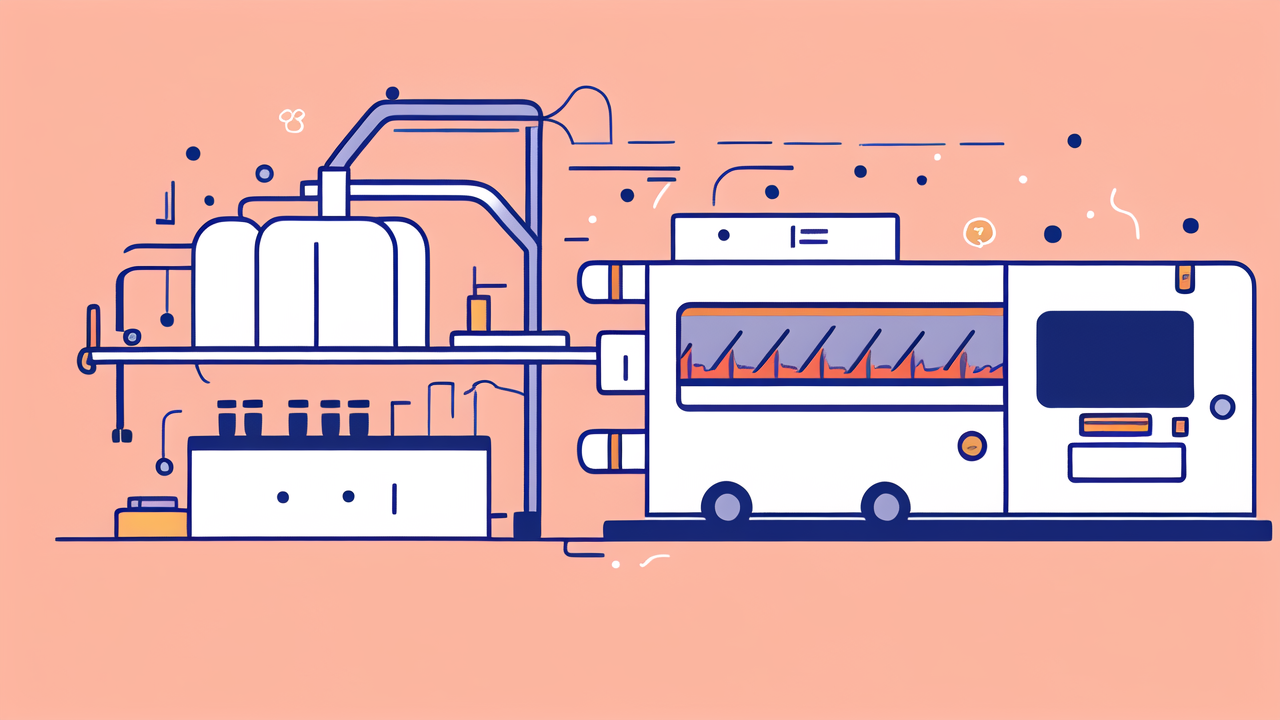
One common method is the free-fall technique. In this process, molten glass drops through a tall tower. As it falls, surface tension shapes the glass into perfect spheres. Another method uses rotating plates. The molten glass is poured onto these plates, and centrifugal force shapes it into balls.
After forming, the balls need to cool down. This cooling process is crucial. It determines the hardness and durability of the final product. Once cooled, the balls go through quality checks. They're sorted by size and checked for any defects. Only perfect spheres make it to the final product.
Technological Advancements in Glass Ball Manufacturing
Technology has greatly improved glass ball production in recent years. New furnaces offer better temperature control. This leads to more uniform glass balls and lower energy costs. Automation has also made the process more precise and efficient.
Advanced materials and coatings have expanded the use of glass balls. Some coatings make the balls more resistant to chemicals. Others improve their optical properties. There's even research into using 3D printing to create custom glass ball designs.
Artificial intelligence is now being used in production. It helps predict and prevent defects, ensuring higher quality. Manufacturers are also focusing on sustainability. They're finding ways to use less energy and recycle glass waste. These advancements are making glass ball production more efficient and eco-friendly.
Applications and Case Studies
Innovative Uses of Glass Balls in Industrial Applications
Glass balls are finding new and exciting uses in industry. In water treatment, they act as a filter media. They can remove tiny impurities from water effectively. The cosmetic industry uses them in scrubs and as carriers for active ingredients. In construction, glass balls are added to insulation materials.
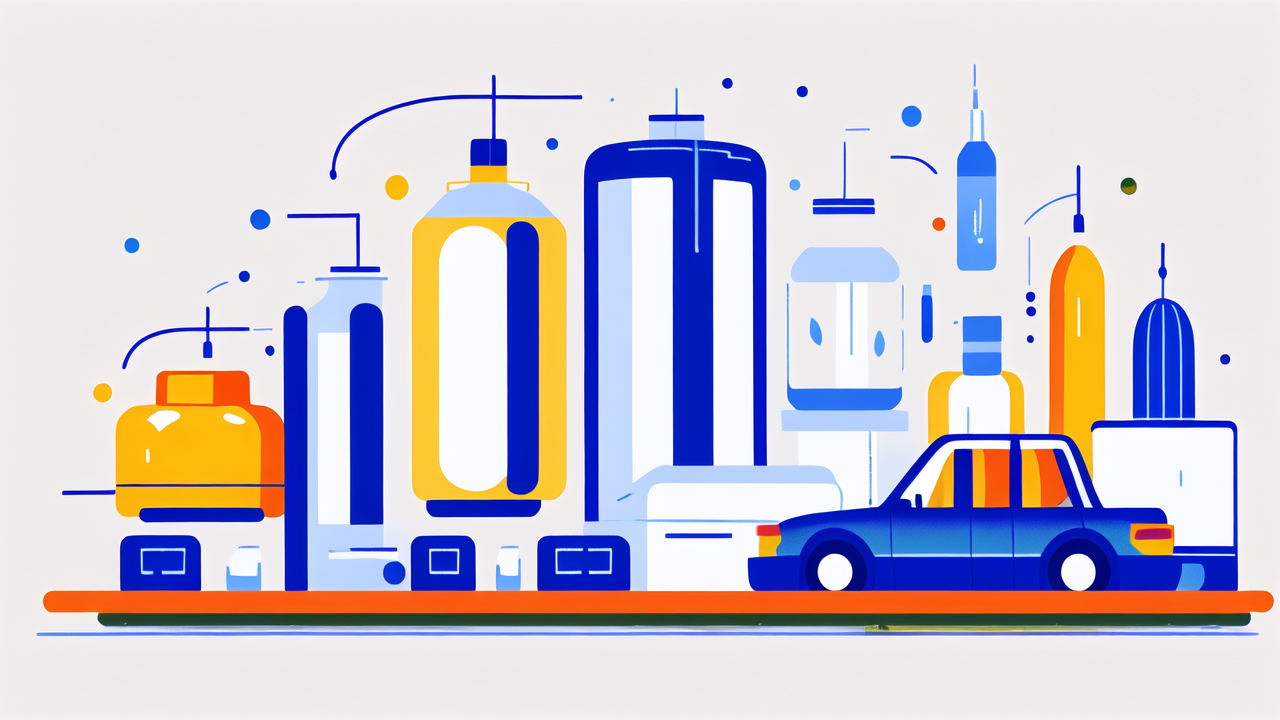
Aerospace companies use glass balls in composite materials for aircraft parts. This makes planes lighter but still strong. In solar energy, glass balls help collect and transfer heat more efficiently. Some companies are even using glass balls in 3D printing as a support material.
Medical researchers are exploring glass balls for targeted drug delivery. In electronics, they're used to create flexible screens and touchscreens. Car makers are using them in smart coatings. These coatings can help cars clean themselves or prevent ice buildup.
Success Stories: Australian Manufacturers and Their Glass Ball Solutions
Australian companies are doing great things with glass ball technology. A company in Perth created a new filtration system for mining. It uses glass balls to clean water more efficiently. This system helps mines use less water and reduce their environmental impact.
A Melbourne firm made special paints with glass balls for road markings. These paints make roads much safer at night. They reflect light better and last longer than traditional paints. In Adelaide, a solar panel maker uses glass balls to improve their panels. The balls help the panels capture more sunlight and produce more energy.
A Sydney company makes glass ball products for drug companies. Their innovations have improved how medicines are made and delivered to patients. These stories show how glass ball technology is helping Australian businesses grow and innovate.