Understanding Laser and Diamond Grinders: An Overview
The Basics of Laser Grinding
Laser grinding is a cutting-edge technology that uses high-powered lasers to remove material. It works by focusing a laser beam on the surface to be ground. The intense heat melts or vaporizes the material. This process is precise and can work on various materials. Laser grinding is often used for complex shapes and hard materials. It offers high accuracy and can create smooth finishes. The process is controlled by computer programs for consistency. Laser grinding is non-contact, reducing tool wear. It's ideal for delicate or heat-sensitive materials. However, it requires specialized equipment and trained operators.
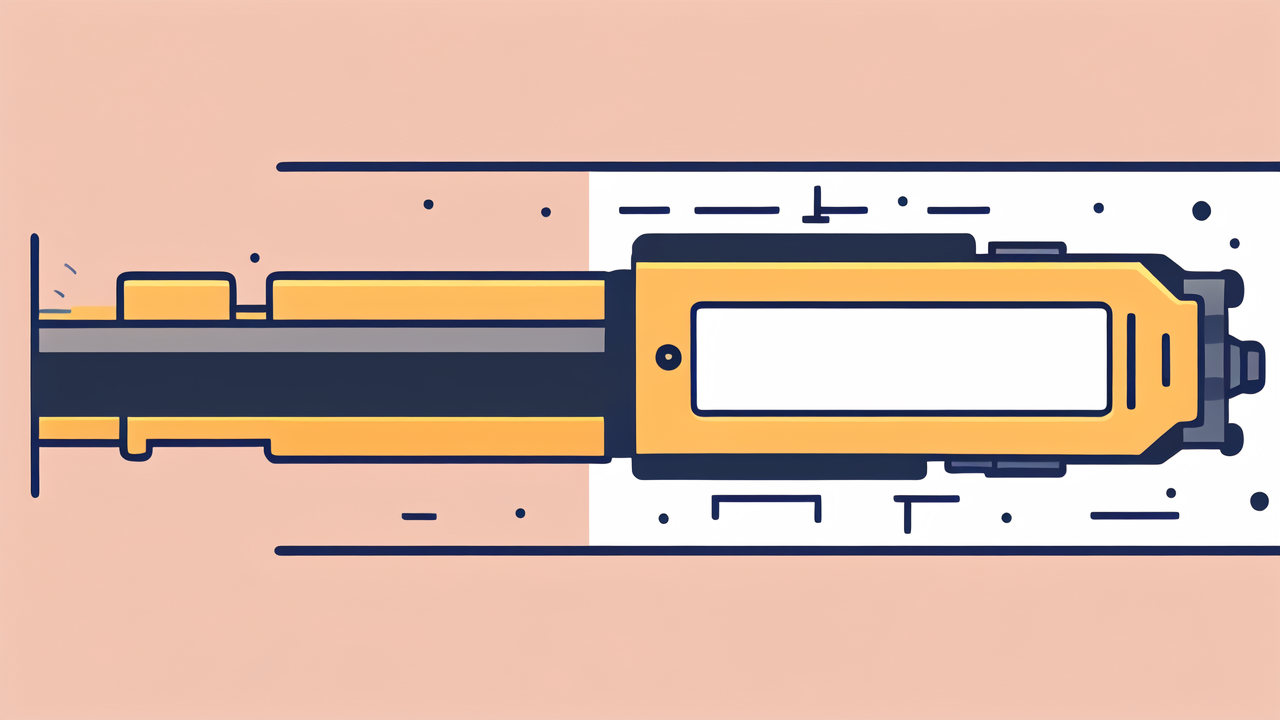
The Basics of Diamond Grinding
Diamond grinding uses abrasive wheels embedded with diamond particles. These wheels rotate at high speeds to remove material. The diamonds are the hardest natural substance, making them ideal for grinding. This method is effective on hard materials like concrete and stone. Diamond grinding can create flat, smooth surfaces quickly. It's often used in construction and manufacturing. The process can be wet or dry, depending on the application. Wet grinding reduces dust and heat. Dry grinding is faster but produces more dust. Diamond grinding is versatile and can handle large areas efficiently. It's a popular choice for floor preparation and surface finishing.
Comparative Analysis: Laser vs. Diamond Grinders
Laser and diamond grinders each have unique strengths. Laser grinders excel in precision and complex shapes. They're ideal for small, intricate work. Diamond grinders are better for large, flat surfaces. They're more efficient for bulk material removal. Laser grinders have no tool wear, while diamond wheels need replacement. Laser grinding is cleaner but requires more energy. Diamond grinding is more versatile across industries. Cost-wise, laser equipment is more expensive initially. However, it may be more economical for certain specialized tasks. Diamond grinding has lower upfront costs but ongoing wheel replacement. The choice depends on the specific application and material. Some industries use both methods for different stages of production.
Laser Grinding Techniques and Applications in Industry
Advantages of Laser Grinding for Manufacturing
Laser grinding offers several key advantages in manufacturing. It provides exceptional precision, crucial for high-tech industries. The non-contact nature reduces material stress and deformation. This is vital for delicate components like those in electronics. Laser grinding can work on materials too hard for traditional methods. It's ideal for ceramics, composites, and advanced alloys. The process is highly repeatable, ensuring consistent quality. Automation is easily integrated, improving efficiency and reducing labor costs. Laser grinding produces less waste and can be more environmentally friendly. It allows for rapid prototyping and small batch production. The flexibility of laser systems means quick changes between tasks. This makes it suitable for customized manufacturing needs.
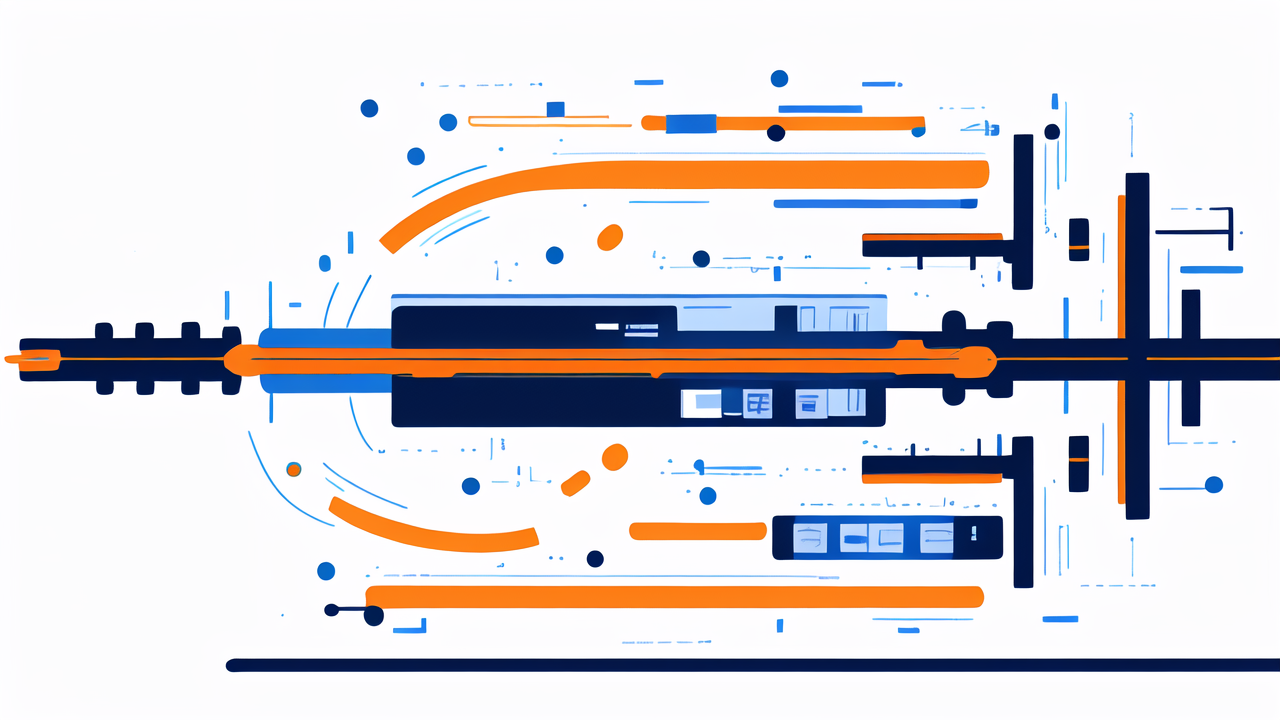
Applications of Laser Grinding in Various Industries
Laser grinding finds applications across diverse industries. In aerospace, it's used for turbine blade repair and component finishing. The medical industry uses it for implant surface texturing and surgical tool production. In electronics, laser grinding creates micro-channels and circuit board vias. The automotive sector employs it for precision engine part manufacturing. Laser grinding is crucial in the production of cutting tools and dies. It's used in the jewelry industry for intricate designs and stone setting. In optics, it helps create precise lenses and mirrors. The semiconductor industry relies on laser grinding for wafer processing. It's also used in the energy sector for solar panel and fuel cell components. Laser grinding is valuable in research for creating custom scientific instruments.
Innovative Laser Grinding Techniques and Their Benefits
New laser grinding techniques are constantly emerging. Ultrafast lasers can now perform 'cold' ablation, reducing heat effects. This is beneficial for heat-sensitive materials. Hybrid systems combining lasers with traditional grinding are gaining popularity. They offer the benefits of both methods. Adaptive optics allow for real-time beam shaping and focusing. This improves accuracy and enables complex 3D grinding. Multi-beam systems increase processing speed for larger areas. Laser-induced plasma techniques can clean surfaces during grinding. Pulsed laser deposition allows for precision material addition during grinding. These innovations expand the capabilities of laser grinding. They make it suitable for an even wider range of applications. The benefits include improved quality, faster processing, and new material possibilities.
Diamond Grinding Techniques and Applications in Australia
Advantages of Diamond Grinding for Industrial Use
Diamond grinding offers significant benefits in industrial applications. It's highly effective for large-scale surface preparation. This makes it ideal for concrete floors in warehouses and factories. Diamond grinding provides excellent material removal rates. It can quickly level uneven surfaces and remove coatings. The process creates a smooth, durable finish that's easy to maintain. It's environmentally friendly, often using water instead of chemicals. Diamond grinding reduces dust compared to other abrasive methods. This improves workplace safety and cleanliness. The technique is versatile, working on concrete, stone, and metal surfaces. It can achieve various levels of smoothness for different needs. Diamond grinding is cost-effective for large areas due to its speed and durability.

Applications of Diamond Grinding in Different Sectors
In Australia, diamond grinding is widely used across various sectors. The construction industry uses it for concrete floor preparation and polishing. It's essential in road maintenance for smoothing and texturing pavements. The mining sector employs diamond grinding for equipment maintenance and ore processing. In manufacturing, it's used for precision finishing of metal components. The stone and tile industry relies on diamond grinding for shaping and polishing. It's crucial in the water treatment sector for maintaining water pipes and tanks. Diamond grinding is used in aerospace for preparing surfaces for coating. The automotive industry uses it for engine block resurfacing. In agriculture, it helps maintain and repair heavy machinery. The technique is also valuable in historical restoration projects.
Innovative Diamond Grinding Techniques and Their Advantages
Recent innovations have enhanced diamond grinding capabilities. New bond materials increase wheel life and cutting speed. Segmented diamond wheels allow for better cooling and debris removal. Computer-controlled grinding systems improve precision and consistency. Dry ice blasting combined with diamond grinding reduces cleanup time. Nano-diamond particles enable ultra-fine surface finishing. Electrolytic in-process dressing (ELID) grinding enhances precision for hard materials. Vibration-assisted grinding improves efficiency and surface quality. These techniques offer advantages like faster processing and better finishes. They also reduce environmental impact and improve worker safety. The innovations make diamond grinding suitable for more specialized applications. They help maintain Australia's competitive edge in manufacturing and construction.
In conclusion, both laser and diamond grinding technologies offer unique advantages. The choice between them depends on specific industry needs and applications. As these technologies continue to evolve, they promise even greater efficiency and precision. Australian industries are well-positioned to benefit from these advancements in grinding technology.